接着剤は業務用まで含めると500種類以上あると言われています。中にはボンド、
セメダイン、アロンアルファなど、1つの企業の商品名がそのまま代名詞になってい る接着剤もあります。 |
|
接着剤は形態による違い、硬化方法による違いにより次のように分類することができます。これらの形態や硬化方法を知ることで、500種類の接着剤もだいぶ理解が深まってきます。 |
形
態
に
よ
る
分
類
|
[固形] |
…… |
熱で溶かして使う通常は固体の接着剤。ホットメルト型とも言います。 |
[エマルジョン系] |
…… |
水の中に樹脂をコロイド状に分散した水性の接着剤。水分の蒸発
により体積が収縮する「やせ」という現象が起きます。木工用ボンドなどがこの分類に入ります。 |
[溶剤系] |
…… |
シンナーなどの溶剤を使用した接着剤。硬化の際、溶剤の揮発により「やせ」がでます。乾いたらゴム状になる合成ゴム系接着剤などがこの分類に入ります。 |
[無溶剤系] |
…… |
溶剤を使用しない接着剤。化学反応により硬化しますので、硬化の際に
体積の収縮がありません。瞬間接着剤などがこの分類に入ります。 |
硬
化
方
法
に
よ
る
分
類
|
[ホットメルト] |
…… |
熱で溶かして接着し、常温で固体に戻ることを利用します。 |
[乾燥型] |
…… |
水分や溶剤の揮発により硬化します。木工用ボンド、合成ゴム系接着剤などがこの分類に入ります。 |
[湿気硬化型] |
…… |
空気中の湿気と反応し硬化します。瞬間接着剤などがこの分類に入ります。 |
[2液反応硬化型] |
…… |
主剤と硬化剤を化学反応させて硬化します。エポキシ系接着剤などがこの分類に入ります。 |
[UV硬化型] |
…… |
字のごとくUV(紫外線)を照射することで硬化します。
|
[嫌気型] |
…… |
空気に触れている間は硬化せず、空気を遮断することで硬化します。
|
[UV嫌気型] |
…… |
UV硬化型と嫌気型の特性を合わせもち、UVの届かない隙間の奥は嫌気性として硬化し、空気に触れる部分はUV照射によって硬化します。
|
※形態による分類からは、硬化する時に「やせ」が生じるかどうかなどが分かります。
これにより、充填剤として適しているかどうかなどが判断できます。 |
上記の分類で説明したとおり、「木工用ボンド」はエマルジョン系・乾燥型の分類に入ります。硬化時間を短くするためには、水分をいかに早く蒸発させるかがポイントです。
また、「瞬間接着剤」は無溶剤系・湿気硬化型という分類に入ります。すぐにくっつくけれど、 湿気に注意する必要があることが分かります。 |
※ 接着剤の硬化方法を知ることで、その接着剤を使用するために必要な機器が分かります。また、硬化防止のためにどのような対策をすれば良いのかなども分かります。
さらに、製品の組立現場では硬化時間に合わせた効率の良い生産工程を組むことができます。 |
「瞬間接着剤」で物と物をくっつけようとしてもくっつかない。また、くっつけようとしたら物が溶けたなどの経験はないでしょうか? 「瞬間接着剤」は正式には「シアノアクリレート系接着剤」と言います。接着する表面の水を触媒として、室温で瞬間的に硬化します。 |
|
熱、圧着、触媒が不要で強固に硬化することから、さまざまな用
途に使われています。一般には、金属、ゴム、プラスチックなどに適しており、逆にポリプロピレン、ポリエチレン、テフロンなどは不適です。最近ではポリプロピレン、
ポリエチレン専用の瞬間接着剤も販売されています。 |
実際の現場で「瞬間接着剤」の塗布における最大の課題は湿気です。けれども湿気は簡単に発生してしまいます。例えば、湿った空気、触手した際の発汗、冷却された接着剤や部材からの結露、水分を吸収するナイロン系部品の使用、コンプレッサからの圧縮空気などです。ですから、完全に湿気をシャットアウトした容器で塗布する必要があります。 |
また、「瞬間接着剤」は、TVコマーシャルでも「たった1滴で」をアピールしていたように、その性質から多く付けすぎるとなかなか硬化しません。適量の塗布が硬化の決め手になりますので、接着剤の量の管理が重要です。
手作業では、湿気を完全にシャットアウトし、適量の吐出コントロールするのは至難の業です。そこで「ディスペンサ(定量吐出装置)」と呼ばれる装置が活躍します。 |
「瞬間接着剤」用途に最適なタイムパルス式コントローラーもあります。また、少量吐出を正確かつ確実にするための多様な瞬間接着剤対応ノズルも用意されています。
ぜひ1度試されてはいかがでしょうか。
詳細はこちらへ |
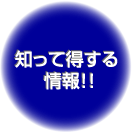 |
銀ペーストは1本当り約2.2g削減で大幅のコストダウン効果
ディスペンサの液剤に銀ペーストを使用している方に朗報です。「SETシリンジ」は、使用後のシリンジ内の銀ペースト残量を0.1%以下にすることが
できます。これにより、従来製品よりシリンジ1本当りの液剤廃棄量を1/8相当に削減します。例えば、シリンジの月間使用本数が1,000本の場合、お金に換算すると月間
約30万円のコストダウンとなります(1本分で約300円)。年間に直すとなんと360万円 以上のコストダウンとなります。
|
 |
メールマガジン第2回目のテーマは……
「接着剤の強さと万一のトラブル対処法」
ご期待ください! |